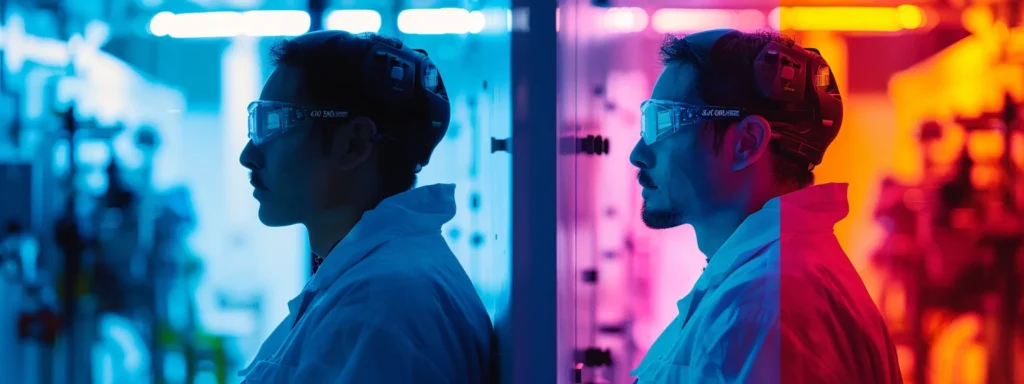

ISO 9001 vs. AS9100: Key Differences in Quality Certifications
When it comes to quality management certifications, many organizations struggle to choose between ISO 9001 and AS9100. Understanding these differences can be critical for effective risk management and ensuring compliance with industry standards. This article will explore key aspects of both certifications, including their distinct focuses, the advantages they offer, and the certification processes involved. Readers will gain insights that can enhance their quality assurance strategies and support their organization‘s motivation towards continuous improvement. Ultimately, this content aims to clarify which certification best suits their configuration management needs.
Understanding ISO 9001 Certification
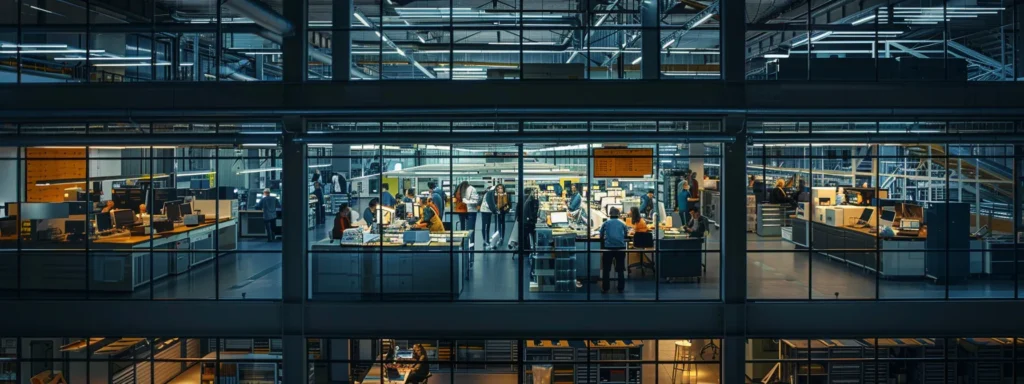
ISO 9001, part of the ISO 9000 family, establishes the framework for quality management systems, aimed at enhancing regulatory compliance and customer satisfaction. Key principles include a strong focus on customer orientation, continual improvement, and process approach. Various industries, including aerospace and manufacturing, utilize ISO 9001 to fulfill contracts and ensure consistent quality in products and services.
Defining ISO 9001 and Its Objectives
ISO 9001 represents an international standard aimed at establishing an effective quality managementsystem. Its primary objective is to enhance customer satisfaction by ensuring that organizations consistently deliver products and services that meet regulatory requirements and quality benchmarks. This standard emphasizes the importance of traceability throughout the production process, enabling organizations to maintain quality control and address issues in real-time, thereby reducing the risk of non-compliance and enhancing overall performance.
In addition to customer satisfaction, ISO 9001 incorporates essential elements like risk assessment and continual improvement. Organizations adopting this standard are encouraged to identify potential risks and implement strategies to mitigate them, fostering a more resilient operational framework. By aligning with practises such as those found in ISO 45001, organizations can create a comprehensive approach to quality and safety, ensuring not only compliance with industry standards but also delivering added value to clients in highly regulated sectors, including aerospace and manufacturing. ISO 9001 certification helps companies demonstrate their commitment to industry standards and customer satisfaction.
Key Principles of ISO 9001
The key principles of ISO 9001 focus on establishing a solid foundation for effective quality management within an organization. Organizations that adopt this standard emphasize customer satisfaction through consistent delivery of products and services that adhere to regulations and quality benchmarks. Fundamental practices, such as conducting internal audits, help organizations identify areas for improvement, ensuring alignment with both customer expectations and regulatory requirements.
Another essential principle is the commitment to continual improvement, which encourages organizations to proactively assess risks and implement strategies to address them. This proactive approach not only enhances operational performance but also prepares organizations to adapt to changes in standards, like IATF 16949, which is particularly relevant in the automotive industry. By integrating these principles, organizations can create a robust framework that not only meets compliance demands but also fosters a culture of quality and accountability.
Common Industries Utilizing ISO 9001
ISO 9001 certification is widely utilized across various industries, reflecting its adaptability and significance in enhancing quality management. The manufacturing sector frequently relies on this standard to optimize their supply chain processes, ensuring that products consistently meet customer expectations and regulatory requirements. For instance, organizations in the medical device field leverage ISO 9001 for rigorous audit processes that focus on verification and validation, ultimately improving the overall customer experience and safety in their offerings.
Another prominent industry utilizing ISO 9001 is aerospace, where quality control is paramount. Companies in this sector utilize the standard to implement systematic practices that enhance traceability and compliance throughout their operations. By establishing a strong quality management framework, these organizations not only streamline their supply chain but also bolster confidence in their products, which is essential for meeting both customer demands and industry specifications.
Examining AS9100 Certification
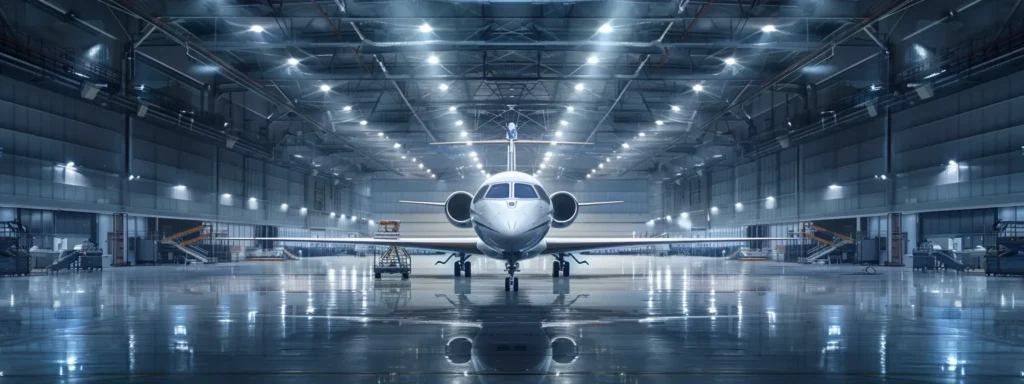
AS9100 is a crucial certification in the aerospace sector, designed to enhance safety and quality management practices. This standard emphasizes core principles such as rigorous training, thorough inspection processes, and effective gap analysis. Various sectors, especially aerospace manufacturers, benefit significantly from AS9100 compliance, ensuring they meet stringent requirements and maintaining operational excellence.
Defining AS9100 and Its Purpose in Aerospace
AS9100certification serves as a key standard within the aerospace industry, aimed at advancing safety and quality management practices. Its implementation provides organizations with a framework that emphasizes efficient evaluation processes, rigorous training, and thorough inspection methods. By prioritizing these elements, companies can enhance their operational knowledge, leading to improved productivity and a more streamlined approach to managing quality within their operations.
This certification also offers a competitive advantage by ensuring that aerospace manufacturers meet stringent industry requirements. Organizations that adopt AS9100 can expect heightened efficiency in their supply chains, bolstering confidence in their products. By integrating these practices, companies not only meet regulatory demands but also deliver on customer expectations, resulting in improved safety and satisfaction throughout the aerospace sector.
Core Principles That Distinguish AS9100
The core principles of AS9100 emphasize standardization and a structured approach to quality management specifically within the aerospace sector. This certification builds on the foundations of ISO 9001 by incorporating additional requirements that enhance confidence in products and services. With a focus on the Plan-Do-Check-Act (PDCA) methodology, organizations are encouraged to apply a cycle of continual improvement, ensuring consistent adherence to industry-specific standards.
Moreover, AS9100 outlines a clearer scope that addresses the unique challenges within the aerospace industry, including rigorous risk management and product traceability measures. This framework not only helps organizations navigate compliance demands but also fosters a culture of accountability and excellence. By incorporating these principles, aerospace manufacturers can demonstrate their commitment to quality, ultimately achieving operational success and client satisfaction.
Sectors That Benefit From AS9100 Compliance
Various sectors benefit significantly from AS9100 compliance, particularly those within the aerospace industry. Organizations adhering to this certification enhance their quality management practices and elevate their quality control measures. Companies can better manage risk and maintain stringent documentation standards, ultimately leading to improved operational efficiency and reliability in their products and services.
Apart from aerospace manufacturers, the defense and space sectors also reap advantages from AS9100certification. These industries face rigorous compliance demands and benefit from the structured approach AS9100 provides for quality management. By adopting this standard, organizations can ensure comprehensive oversight of quality control processes, fostering a culture of safety and reliability that meets the expectations of stakeholders and regulatory bodies alike.
Key Differences Between ISO 9001 and AS9100
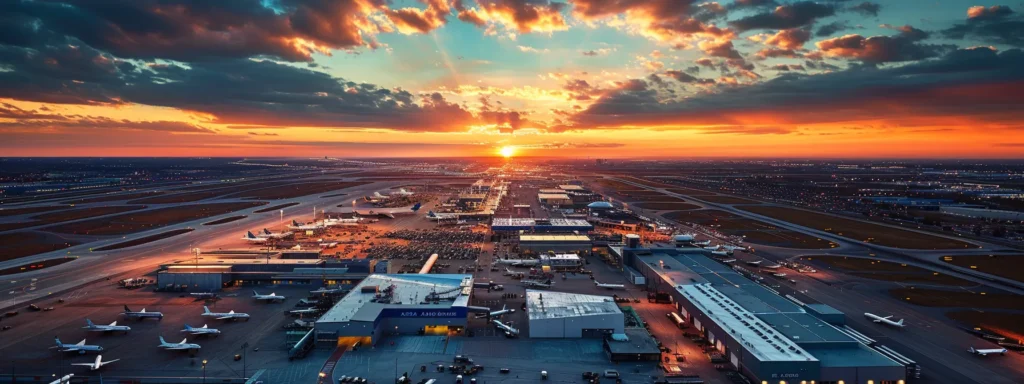
The differences between ISO 9001 and AS9100 primarily relate to their scope and applicability, with AS9100 placing a stronger emphasis on risk management tailored for the aerospace sector. Furthermore, audit requirements vary between these standards, as AS9100 demands more rigorous documentation and processes, impacting resource allocation and stakeholder communication. This section will explore these distinctions in detail.
Scope and Applicability of Each Standard
The scope of ISO 9001 centers on establishing a robust quality managementsystem applicable across various industries. This standard focuses on customer satisfaction by ensuring that organizations consistently meet quality requirements. In contrast, AS9100 narrows its applicability specifically to the aerospace sector, incorporating additional requirements to address the unique uncertainty and compliance demands faced by organizations in this field.
AS9100 is designed to enhance risk management and traceability within the quality managementsystem, emphasizing factors critical for aerospace manufacturers. While ISO 9001 lays the groundwork for quality systems, AS9100 builds upon it to provide a tailored approach that meets stringent industry standards. This distinction allows organizations in aerospace to not only comply with regulatory frameworks but also improve quality outcomes, directly benefiting their customers.
Emphasis on Risk Management in AS9100
AS9100 places a strong emphasis on risk management, highlighting its significance in ensuring quality and safety within the aerospace sector. This standard requires organizations to implement effective measurement techniques to identify and assess potential risks throughout their processes. By engaging in rigorous root cause analysis, companies can establish a framework that not only mitigates risks but also enhances their overall operational efficiency and compliance with industry regulations.
Furthermore, AS9100 incorporates specific practices for calibration and documentation, ensuring that measurements are accurate and consistent in all operations. This structured approach fosters mutual recognition among stakeholders, reinforcing confidence in the quality of products and services offered. As organizations navigate the complexities of the aerospace sector, having robust risk management strategies helps them safeguard personal data and meet the stringent expectations set by regulators and customers alike.
Audit Requirements for ISO 9001 vs. AS9100
The audit requirements for ISO 9001 focus on assessing the effectiveness of the quality managementsystem within an organization. These audits typically involve evaluating documentation, processes, and evidence that demonstrate compliance with regulatory standards. For laboratories and research facilities, maintaining this evidence is critical for international accreditation forum recognition, as it showcases a commitment to quality and continuous improvement in their operations.
In contrast, AS9100 amplifies the audit process with more rigorous expectations tailored to the aerospace industry. The emphasis on detailed documentation and stringent inspection practices requires organizations to provide comprehensive evidence of compliance, particularly regarding risk management and traceability. This heightened scrutiny not only ensures that organizations meet industry standards but also fosters greater confidence among stakeholders in the safety and reliability of aerospace products.
Advantages of ISO 9001 and AS9100 Certifications
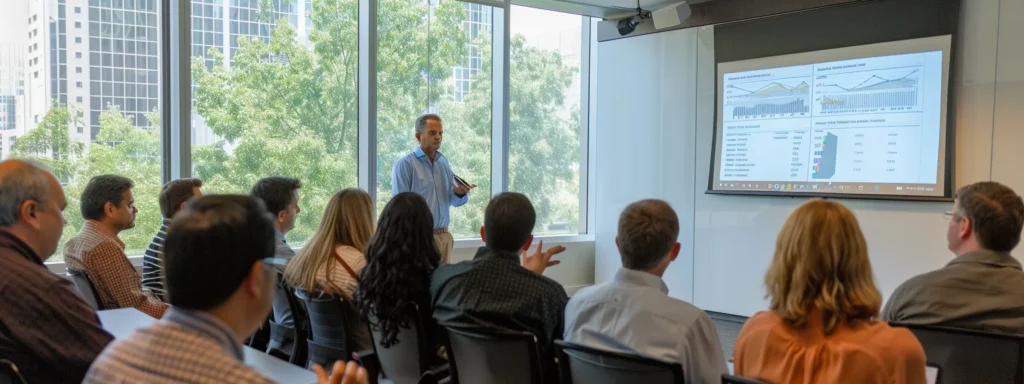
ISO 9001 offers significant advantages for organizational improvement, facilitating streamlined processes and enhanced customer satisfaction. In contrast, AS9100 provides specialized quality assurance benefits crucial for the aerospace and manufacturing sectors. This section will highlight how ISO 9001 contributes to operational excellence, while AS9100 ensures compliance with rigorous standards, reinforcing the importance of accreditation, such as the United Kingdom Accreditation Service and ISO 13485.
Organizational Improvement Through ISO 9001
ISO 9001 certification supports organizational improvement by establishing standardized processes that enhance efficiency and effectiveness. By implementing a quality managementsystem, organizations can systematically identify areas requiring enhancements, leading to reduced waste and improved resource utilization. For instance, a manufacturing firm may discover through internal audits that a particular production method is less efficient, allowing them to adjust operations accordingly and boost overall productivity.
Moreover, ISO 9001 fosters a culture of continuous improvement, encouraging all employees to contribute to quality initiatives. Organizations that engage their teams in quality practices often witness increased employee satisfaction and retention as a result of their involvement in meaningful process enhancements. An IT service provider, for example, may implement feedback loops that empower staff to address client concerns proactively, ultimately leading to higher client satisfaction and loyalty.
Quality Assurance Benefits Provided by AS9100
AS9100certification strengthens quality assurance in the aerospace sector by establishing rigorous standards for safety and reliability. This certification requires organizations to implement comprehensive quality management practices, resulting in enhanced oversight of their production processes. For example, aerospace manufacturers benefit significantly from improved risk management strategies that ensure compliance with both regulatory demands and client expectations, safeguarding both operational integrity and customer trust.
Furthermore, the focus on precise documentation and meticulous inspection protocols under AS9100 helps companies maintain consistent quality across all operations. This structured approach not only facilitates better product traceability but also bolsters accountability throughout the supply chain. By adhering to these high standards, organizations can demonstrate their commitment to excellence, ultimately leading to increased market competitiveness and customer satisfaction in a demanding industry.
Comparing Certification Processes
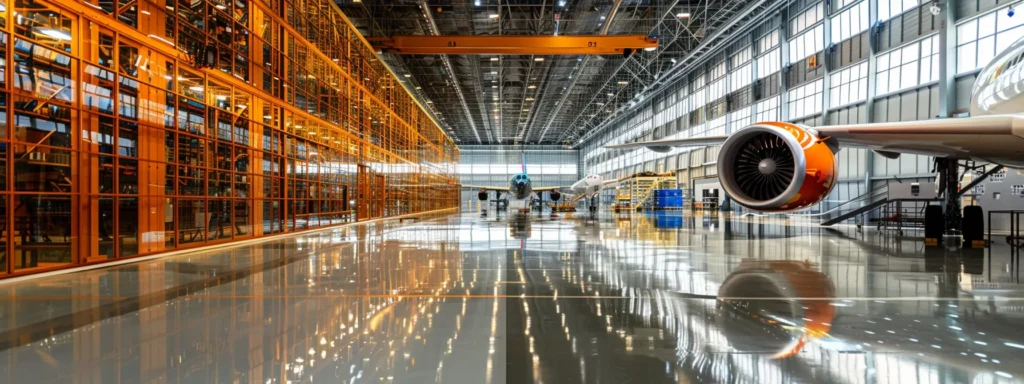
Comparing Certification Processes
Achieving ISO 9001 certification involves specific steps, including developing a quality managementsystem, conducting internal audits, and preparing for external assessments. In contrast, attaining AS9100certification requires organizations to adopt aerospace-specific practices and focus on rigorous documentation. Both certifications come with unique cost implications, which will be explored in more detail in the following sections.
Steps to Achieving ISO 9001 Certification
Achieving ISO 9001 certification begins with the development of a comprehensive quality managementsystem (QMS) tailored to the organization’s specific processes and goals. Organizations must engage in thorough documentation of their procedures, policies, and objectives, which lays the foundation for consistent quality outcomes. Internal audits play a crucial role at this stage, as they help identify gaps in compliance and provide insights for necessary improvements.
Once the QMS is in place and internal audits confirm its effectiveness, organizations prepare for external assessments conducted by certified auditors. This involves ensuring that all documentation is complete and that staff members are trained to understand and implement the quality management practices. Successful completion of this assessment culminates in the awarding of ISO 9001 certification, affirming the organization‘s commitment to quality and regulatory compliance in delivering products and services.
Steps to Attain AS9100 Certification
To attain AS9100certification, organizations must first develop a robust quality managementsystem (QMS) specifically tailored to the aerospace industry. This process includes creating detailed documentation that outlines policies, procedures, and quality objectives essential for compliance with AS9100 requirements. Engaging employees in this preparation phase is crucial, as it fosters a culture of quality and accountability throughout the organization, ensuring everyone understands their role in meeting safety and performance standards.
Following the establishment of a comprehensive QMS, organizations need to conduct internal audits to identify any gaps in compliance and areas for improvement. This audit process assesses if the QMS aligns with AS9100 criteria and whether the organization‘s practices comply with industry-specific requirements. After addressing any identified deficiencies, organizations prepare for external audits conducted by certified AS9100 auditors, ultimately leading to the awarding of the certification which signifies their commitment to quality and safety in aerospace operations.
Cost Implications of Each Certification Route
Obtaining ISO 9001 certification typically involves costs related to the development and implementation of a quality managementsystem. Organizations must invest in training staff, updating documentation, and conducting internal audits to ensure compliance. These expenses can vary widely depending on the size and complexity of the organization but are generally manageable for most businesses seeking to improve their quality management practices.
In contrast, the pathway to AS9100certification often incurs higher costs given the specialized requirements outlined for the aerospace industry. Organizations must implement more rigorous documentation and risk management protocols, along with intensive training to meet industry standards. The need for detailed compliance audits and inspections can further increase the financial investment, making it essential for aerospace firms to carefully assess the implications of pursuing AS9100certification within their operational budget.
Practical Examples of ISO 9001 and AS9100 Application
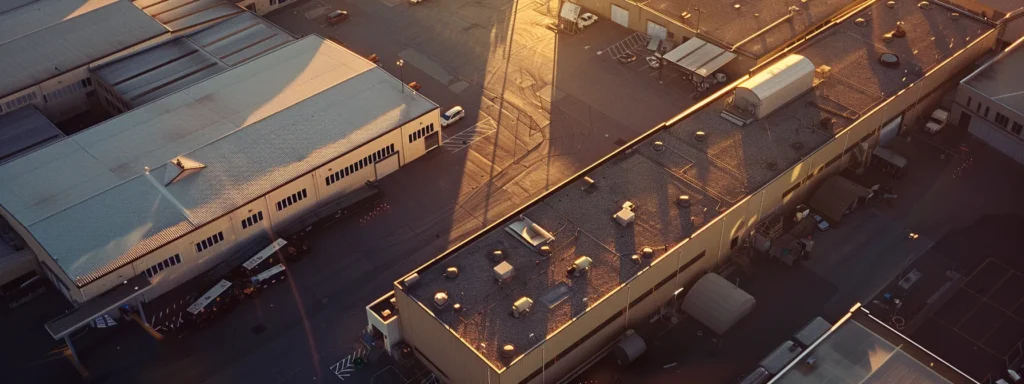
ISO 9001 success stories showcase how organizations improve operational efficiency through structured quality management systems. Real-world implementations of AS9100 highlight advancements in aerospacesafety and reliability. Additionally, lessons learned from organizations utilizing both standards provide valuable insights into bridging gaps and enhancing compliance. Each case emphasizes the importance of these certifications in driving quality and customer satisfaction.ISO 9001 success stories
Case Studies Showing ISO 9001 Success
One notable case study demonstrating the success of ISO 9001 certification involved a mid-sized manufacturing company that sought to improve its operational efficiency. By implementing ISO 9001 standards, the organization established a structured quality management system that streamlined processes and significantly reduced waste. As a result, the company enhanced its overall productivity and achieved higher customer satisfaction ratings, showcasing how adherence to quality management principles can lead to tangible business improvements.
Another example comes from a service-based organization that faced challenges in meeting client expectations consistently. After achieving ISO 9001 certification, the company developed a refined quality management framework that emphasized continuous feedback and performance monitoring. This shift not only led to improved service delivery but also fostered a culture of accountability among employees, ultimately driving results that exceeded client expectations and solidified the organization’s reputation in a competitive market.
Real-World Implementations of AS9100
One notable implementation of AS9100 can be seen in a prominent aerospacemanufacturing company that sought to enhance its production quality and safety measures. By adopting the AS9100 standard, the organization improved its risk management protocols and established stringent documentation practices, which helped to identify potential issues early in the production process. This proactive approach resulted in decreased non-compliance incidents and increased customer trust in the reliability of their products.
Another effective application of AS9100 occurred within a defense contractor that aimed to streamline its quality managementsystem. By integrating AS9100 standards, the company developed a structured framework for conducting thorough inspections and audits throughout its operations. This not only ensured robust compliance with regulatory requirements but also enhanced collaboration across teams, leading to improved efficiencies and higher rates of customer satisfaction in a highly competitive market.
Lessons Learned From Organizations Using Both Standards
Organizations that adopt both ISO 9001 and AS9100 often discover valuable insights about streamlining their quality management systems. For example, a manufacturer in the aerospace sector reported improved operational efficiency after integrating the broader practices of ISO 9001 with the specific requirements of AS9100. This dual approach enabled them to address customer needs while maintaining stringent compliance with industry standards, resulting in higher satisfaction rates among clients.
Another important lesson highlights the significance of fostering a culture of continuous improvement. Companies utilizing both standards find that engaging all employees in quality initiatives leads to better operational outcomes. One defense contractor noted that actively involving team members in identifying issues and proposing enhancements strengthened accountability and contributed to a more effective quality management framework, ultimately benefiting overall performance and safety standards.
Key Takeaways: ISO 9001 vs AS9100 Quality Management
Understanding the distinctions between ISO 9001 and AS9100 is essential for organizations aiming to enhance their quality management systems. ISO 9001 provides a foundational framework applicable across various industries, while AS9100 offers tailored specifications crucial for the aerospace sector. Emphasizing risk management and rigorous documentation, AS9100 drives compliance and boosts confidence in product safety and quality. By recognizing these differences, organizations can make informed decisions about the certification routes that best align with their operational needs and customer expectations.