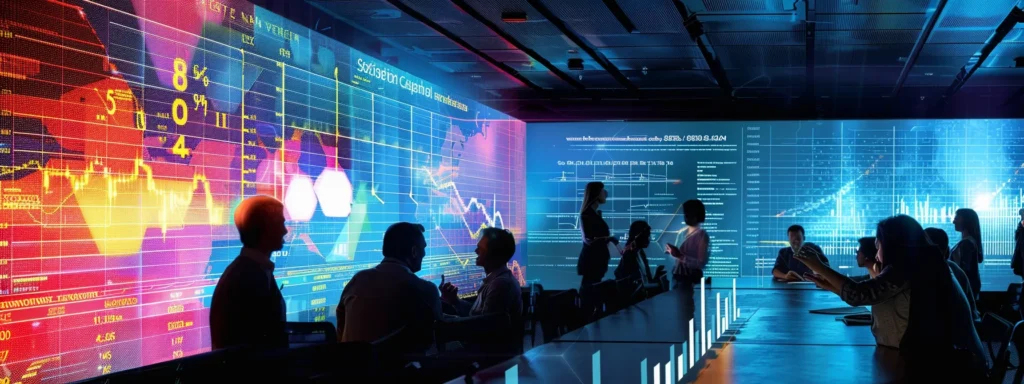
Overcoming Key Challenges in Your ISO 9001 Certification Journey
Achieving ISO 9001 certification is often seen as a straightforward path to enhancing quality control and operational efficiency. Yet, many companies encounter significant challenges along the way. This article will explore common obstacles such as managing leadership commitment, addressing internal audit issues, and understanding documentation requirements. By engaging with this content, readers will uncover strategies to tackle these pain points effectively, enhancing communication and inspection processes to streamline their certification journey.
Identifying Common Obstacles in ISO 9001 Certification Process
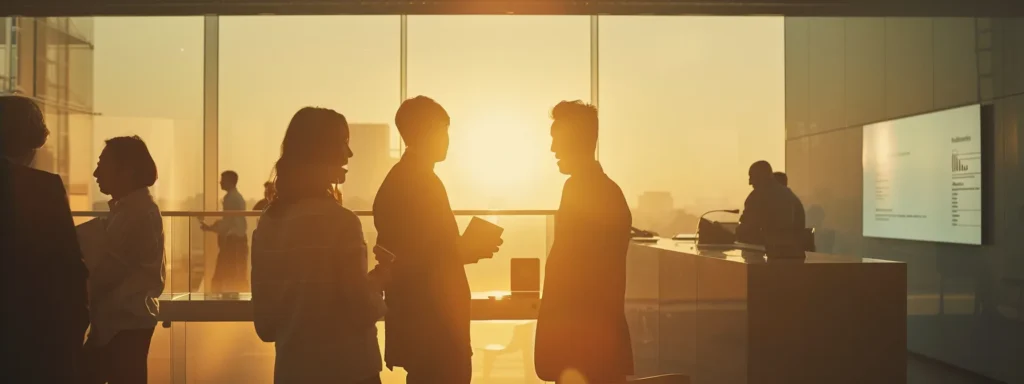
Understanding the complexity of ISO 9001 standards presents a significant hurdle for organizations aspiring for certification. Recognizing employee resistance to change, assessing the need for proper documentation, and evaluating resource constraints and budget limitations are crucial steps in the process. Additionally, analyzing inadequate training and knowledge gaps can further impede effective quality management and problem solving. Each of these topics will provide insights into overcoming these obstacles for successful ISO 9001 certification.
Understanding the Complexity of ISO 9001 Standards
ISO 9001 standards contribute to a robust framework aimed at enhancing customer satisfaction and ensuring high-quality processes. Organizations often face challenges in comprehending the requirements detailed within these standards, especially when integrating them with existing policies. A deeper understanding of how these standards relate to effective automation and collaboration across departments can help streamline the certification process and drive continuous improvement.
Moreover, the complexity of ISO 9001 necessitates a commitment from various organizational levels to fully embrace the quality managementsystem. This commitment is essential not only for meeting certification requirements but also for fostering a culture focused on customer satisfaction. Engaging employees through training and support in interpreting and implementing these standards will ultimately contribute to a successful certification journey and better overall performance.
Recognizing Employee Resistance to Change
Employee resistance to change represents a significant challenge in the ISO 9001 certification process. Many employees may lack confidence in new procedures, leading to reluctance in adopting enhancements within quality management systems. By actively involving team members in internal audits and fostering a sense of ownership in processes, organizations can increase compliance and support, enhancing the implementation of ISO standards.
Assessing the Need for Proper Documentation
Proper documentation is essential for organizations pursuing ISO 9001 certification. It serves as the backbone of a quality managementsystem, guiding processes, practices, and compliance with the International Organization for Standardization requirements. Companies often realize the need for thorough documentation through gap analysis, which identifies discrepancies between current practices and ISO standards. Engaging a consultant can provide additional insight into the best practices for creating and maintaining documentation that enhances efficiency and aligns with the overall objectives of the organization.
Moreover, effective documentation not only ensures compliance but also promotes continuous improvement in quality management. Organizations that clarify their processes and maintain accurate records often experience significant gains in operational efficiency. By investing in proper documentation practices and the expertise of a consultant, companies can minimize errors and create a more transparent work environment that fosters accountability and drives success in their ISO 9001 certification journey.
Evaluating Resource Constraints and Budget Limitations
Resource constraints and budget limitations represent significant challenges when organizations pursue ISO 9001 certification. Many companies, especially in the food industry, often find themselves balancing day-to-day operations with the demands of implementing a robust quality managementsystem. This can lead to difficulties in dedicating sufficient manpower and financial resources to meet the certification requirements. When teams are focused on meeting project management goals, the quality processes necessary for compliance may inadvertently take a backseat.
Conducting thorough research on available resources can alleviate some of these issues. For example, companies should consider leveraging existing systems and personnel to enhance efficiency without incurring additional costs. Utilizing internal expertise fosters a culture of continuous improvement, allowing organizations to maximize their potential while working within budgetary constraints. By addressing resource limitations strategically, businesses can better position themselves for successful ISO 9001 certification and the benefits that come with it.
Analyzing Inadequate Training and Knowledge Gaps
Organizations often face significant challenges related to inadequate training and knowledge gaps during the ISO 9001 certification journey. Employees may harbor fear regarding the implementation process of new methodologies, such as Six Sigma, which can lead to hesitation in fully engaging with the quality managementsystem. Addressing these knowledge deficits requires companies to invest in tailored training programs that clarify standards and expectations while demonstrating the operational benefits of these frameworks.
Effective training directly contributes to overcoming resistance and builds a confident workforce that understands the value of ISO 9001 compliance. Organizations that prioritize ongoing education can create a culture where knowledge sharing becomes a competitive advantage. By equipping employees with the necessary tools to understand and execute quality management practices, businesses not only streamline the certification process but also cultivate a more adaptive and efficient organization.
Managing Leadership Commitment and Engagement
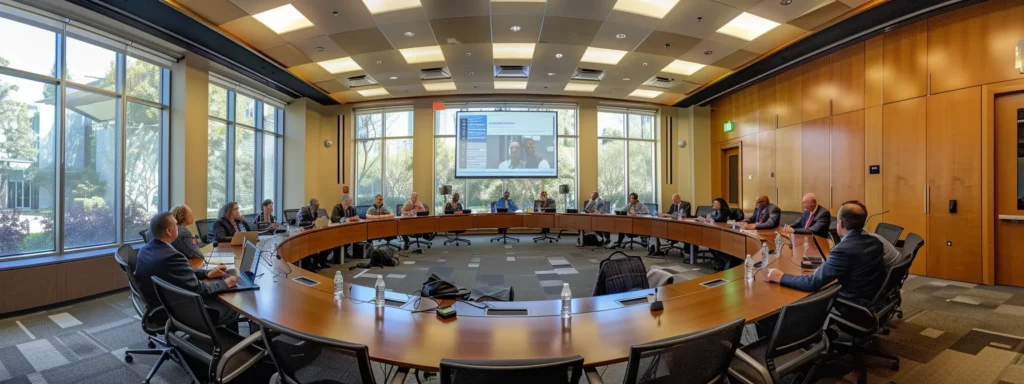
Top management support plays a crucial role in the journey to ISO 9001 certification. Cultivating a quality-driven culture within organizations fosters an environment conducive to regulatory compliance. Encouraging communication and team collaboration aligns ISO 9001 goals with overall business objectives while addressing leadership challenges during implementation. Each of these elements contributes to effective change management, positioning companies for successful professional certification.
Importance of Top Management Support
Top management support is essential for any organization pursuing ISO 9001 certification, especially in the manufacturing sector. When leadership actively promotes standardization efforts, it signals the importance of quality management throughout the organization. This commitment can enhance trust and loyalty among employees, as they understand that the organization prioritizes a reliable and effective quality managementsystem.
Moreover, leaders who leverage analytics during the certification process can identify areas needing improvement and allocate resources appropriately. This proactive approach not only eases the challenges associated with certification but also fosters a culture of continuous improvement. By consistently engaging with employees and demonstrating the value of ISO 9001 standards, top management can ensure the organization remains aligned with its certification goals and can navigate the complexities of quality management successfully.
Cultivating a Quality-Driven Culture in Organizations
Cultivating a quality-driven culture requires the commitment of leadership to prioritize quality management principles throughout the organization. This involves implementing regular evaluations that assess current practices and identifying areas for improvement through root cause analysis. By consistently communicating the importance of standards like ISO 9001 via newsletters and internal communications, leaders can foster employee engagement, ensuring that everyone understands their role in achieving certification success.
Strategic management plays a vital role in establishing a culture that values quality. When top management actively participates in initiatives that promote quality awareness, they set a tone that inspires employees to embrace continuous improvement. Such engagement not only helps in aligning individual efforts with organizational objectives but also empowers teams to take ownership of their contributions towards maintaining a robust quality managementsystem.
Encouraging Communication and Team Collaboration
Effective communication across teams is essential for fostering collaboration that enhances workflow during the ISO 9001 certification journey. Encouraging open dialogue allows human resources and other departments to share insights and strategies that align with quality management objectives. This inclusive approach not only improves operational efficiency but also supports a broader commitment to sustainability by promoting best practices in areas such as food safety.
Leaders should prioritize creating an environment where team collaboration thrives, which directly impacts the skill development of employees. Regular meetings and collaborative projects encourage sharing of knowledge, enabling staff to become more adept at implementing ISO 9001 standards. By addressing potential challenges collectively and encouraging input from all levels, companies can strengthen their quality management systems and move closer to achieving successful certification.
Aligning ISO 9001 Goals With Business Objectives
Aligning ISO 9001 goals with business objectives is fundamental to developing an effective quality managementsystem that resonates throughout the organization. When companies integrate regulation requirements into their overarching strategy, they create a unified approach that enhances customer satisfaction while streamlining operations in logistics. For example, a manufacturing firm that aligns its ISO objectives with production goals can reduce waste and improve throughput, directly benefiting both the bottom line and customer experience.
Effective communication from leadership plays a critical role in this alignment. By regularly communicating the importance of ISO 9001 standards in relation to the company’s strategic goals, leadership helps employees understand the value of their contributions to compliance initiatives. This clarity enables teams to prioritize quality management practices, ultimately cultivating a culture where regulations become a part of everyday operations rather than an added burden, leading to a more seamless certification journey.
Overcoming Leadership Challenges During Implementation
Overcoming leadership challenges during the ISO 9001 certification process requires a proactive approach to risk assessment and management. Leaders must recognize the potential risks associated with adopting new quality management systems, as these can impact the organization’s reputation if not addressed effectively. Engaging stakeholders at every level allows for a collaborative environment where concerns can be voiced and solutions developed, creating a culture that supports both compliance and continuous improvement.
To foster commitment from leadership, it is essential to promote awareness of how ISO 9001 standards align with the organization‘s strategic goals. This alignment not only addresses the perceived risks involved but also highlights the benefits of a strong quality managementculture. By demonstrating to stakeholders how adherence to these standards can enhance operational efficiency and strengthen the company’s reputation, organizations can secure the vital support needed for a successful certification journey.
Addressing Internal Audit and Evaluation Challenges
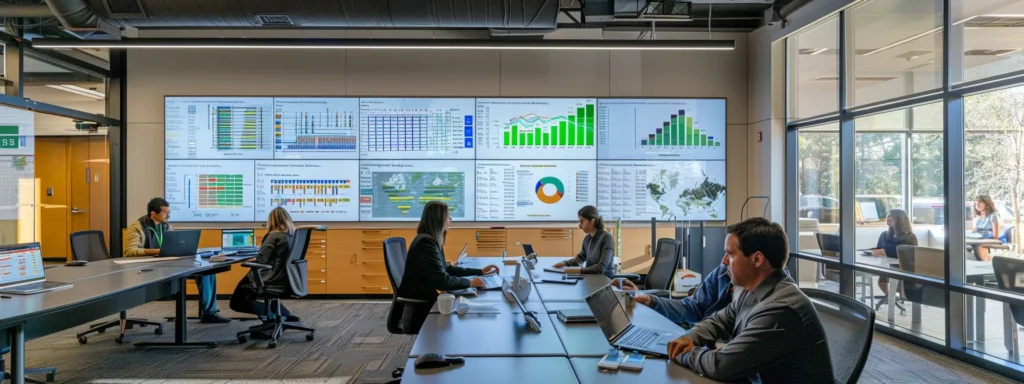
Establishing an effective internal auditsystem is essential for maintaining quality management systems and ensuring compliance with ISO 9001 standards. Organizations must ensure objectivity and independence in audits while effectively handling nonconformities and implementing corrective actions. Streamlining continuous improvement processes and addressing compliance challenges post-certification are vital for enhancing risk management and productivity in supply chain management. Each of these aspects provides practical insights to support a successful certification journey.
Establishing an Effective Internal Audit System
Establishing an effective internal auditsystem is critical for maintaining a strong quality assurance framework in alignment with ISO 9001 standards. Organizations must ensure that their auditing infrastructure is built on a foundation of leadership support and adequate knowledge among team members. This involves providing training to auditors, which enhances their skills and confidence, thereby promoting a more thorough evaluation of processes and practices.
Moreover, the internal audit process should not only focus on identifying nonconformities but also emphasize continual enhancement. By integrating principles from ISO 22000, organizations can develop auditing strategies that not only meet food safety standards but also reinforce overall quality management efforts. Engaging employees in the audit process fosters a culture of accountability and encourages proactive contributions to compliance initiatives, resulting in a robust quality managementsystem that supports certification goals.
Ensuring Objectivity and Independence in Audits
Ensuring objectivity and independence in audits is critical for organizations pursuing ISO 9001 certification, especially in sectors like medical devicemanufacturing. Proper training for internal auditors equips them with the necessary skills to evaluate processes without bias, fostering an atmosphere of transparency. By maintaining clear separation between audit responsibilities and operational roles, organizations can enhance their understanding and effectively manage their safety management system.
An effective audit process requires open communication and a commitment to unbiased evaluations. Organizations can strengthen the credibility of their internal audits by engaging external experts occasionally, providing a fresh perspective on compliance with ISO standards. This approach not only affirms the integrity of audit findings but also promotes a culture of continuous improvement, allowing organizations to align their quality objectives with broader business goals.
Handling Nonconformities and Corrective Actions
Handling nonconformities and implementing corrective actions are critical steps in the ISO 9001 certification process. When an internal audit reveals deviations from established quality standards, organizations must promptly address these issues to maintain compliance and improve their quality management systems. For example, if a manufacturer identifies a recurring defect in its production line, taking immediate corrective action can help prevent future occurrences and demonstrate a commitment to quality improvement.
Effective management of nonconformities requires a structured approach that includes documenting the issues, analyzing root causes, and executing corrective actions. Organizations benefit from involving cross-functional teams in this process, as diverse insights can lead to more effective solutions. By ensuring that the audit findings are addressed thoroughly, companies not only enhance their quality assurance processes but also build a culture of accountability that reinforces ongoing commitment to ISO 9001 standards.
Streamlining Continuous Improvement Processes
Streamlining continuous improvement processes is vital for organizations aiming for ISO 9001 certification. It involves integrating quality management practices into daily operations to ensure consistent monitoring and enhancement of processes. For instance, businesses can adopt methodologies such as Plan-Do-Check-Act (PDCA) to systematically identify areas for improvement, implement solutions, and evaluate results, fostering a culture of ongoing refinement.
Moreover, leveraging digital tools can significantly facilitate this continuous improvement journey. Organizations can use software solutions to track key performance indicators and analyze data in real-time, enabling them to respond quickly to deviations from quality standards. By prioritizing a streamlined approach, companies can enhance their internal audit effectiveness and promote a commitment to quality, thereby reinforcing their path toward successful ISO 9001 certification.
Obstacle of Maintaining Compliance Post-Certification
Maintaining compliance post-certification poses a substantial challenge for organizations, as the initial effort to achieve ISO 9001 certification can sometimes lead to complacency. Many businesses may find it difficult to keep up with ongoing requirements, resulting in potential nonconformities that could jeopardize their certified status. Regular internal audits and evaluations become critical in these instances, ensuring that quality management practices remain effective and aligned with ISO standards throughout the lifecycle of the certification.
To combat the risk of diminished compliance, organizations should establish a robust monitoring system. This system can include scheduled reviews, performance metrics, and employee training to reinforce the importance of continual adherence to ISO 9001 standards. By proactively addressing quality management processes and fostering a culture of accountability, companies can not only maintain their certification but also enhance overall operational efficiency and customer satisfaction.
Understanding the Role of Documentation and Process Mapping
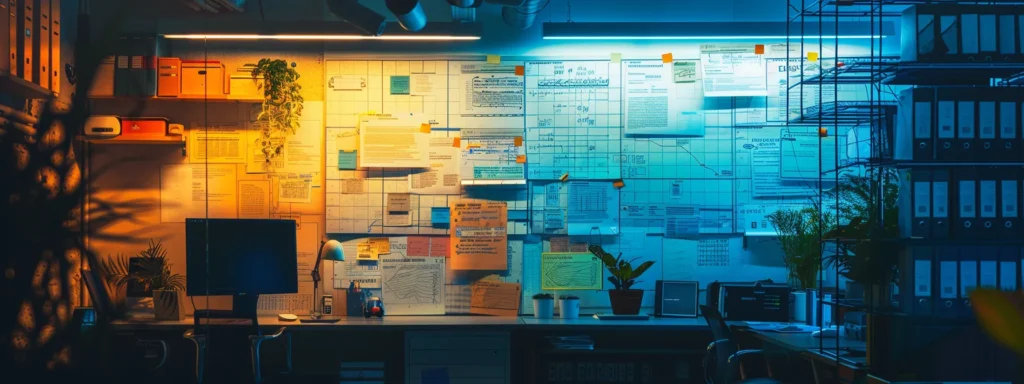
Developing effective Standard Operating Procedures (SOPs) is crucial for organizations pursuing ISO 9001 certification, as it establishes a consistent framework for quality management. Comprehensive process mapping provides clarity in operations, while balancing flexibility and standardization in documentation ensures efficient practices. Ensuring all employees have access to key documents and addressing common pitfalls in document control are essential steps for success in this certification journey.
Importance of Developing Effective SOPs
Developing effective Standard Operating Procedures (SOPs) is a critical component for organizations pursuing ISO 9001 certification, as these documents serve as the foundation for consistent practice across functions. Clear SOPs ensure that all employees follow standardized methods, reducing variability and enhancing quality control. For example, a manufacturing company can use SOPs to detail each step in its production process, which minimizes the chances of error and facilitates smoother audits.
Moreover, well-structured SOPs contribute to organizational efficiency by streamlining training and onboarding processes. When new hires have access to comprehensive documentation, they can quickly understand operational expectations and uphold compliance with ISO 9001 standards. As organizations encourage adherence to these procedures, they foster a culture of accountability and continuous improvement that ultimately supports their certification goals.
Comprehensive Process Mapping for Clarity
Comprehensive process mapping serves as a vital tool for organizations navigating the complexities of ISO 9001 certification. By visually outlining each step in their operations, companies can identify potential gaps or inefficiencies that could hinder compliance. For example, a manufacturing entity can map its production workflow, revealing where quality checks are missing or where documentation needs to be strengthened, thus facilitating a clearer understanding of operational standards required for ISO compliance.
Furthermore, effective process mapping enhances communication and collaboration among teams, ensuring that every employee understands their role in maintaining quality management systems. When departments can easily reference process maps, they are more likely to adhere to established procedures, reducing the likelihood of errors. By documenting these processes, organizations not only streamline their operational efficiency but also create a foundation for continuous improvement aligned with ISO 9001 requirements.
Balancing Flexibility and Standardization in Documentation
Balancing flexibility and standardization in documentation is essential for organizations pursuing ISO 9001 certification. Companies need to create robust documentation that outlines standard operating procedures while allowing for adaptability to meet changing business needs. For instance, a manufacturing firm may implement standardized procedures for quality checks but should also include criteria for adjusting processes in response to new technologies or market demands, ensuring compliance while maintaining operational agility.
Furthermore, maintaining this balance fosters a culture of continuous improvement. Organizations can encourage employees to provide feedback on existing documentation and process workflows, promoting an environment where employees feel empowered to suggest enhancements. By integrating a systematic approach to documentation that embraces both standardization and flexibility, companies can navigate the complexities of ISO 9001 certification more effectively, leading to improved overall quality management.
Ensuring Access to Key Documents for All Employees
Ensuring that all employees have access to key documents is crucial for organizations striving for ISO 9001 certification. These documents, which include policies, procedures, and training materials, serve as essential resources that guide daily operations and compliance efforts. Providing centralized access through digital platforms or shared networks not only promotes transparency but also empowers employees to adhere to quality management practices, thereby enhancing overall performance and accountability.
Moreover, organizations can mitigate challenges associated with knowledge gaps by implementing document control systems that make it easy for staff to locate and access relevant documentation. Regular training sessions on how to navigate these systems further reinforce the importance of maintaining and using documents effectively. By prioritizing accessibility, companies not only contribute to a culture of continuous improvement but also ensure that every employee plays an active role in achieving ISO 9001 certification success.
Common Pitfalls in Document Control Procedures
One common pitfall in document control procedures is the failure to regularly update and review documents. Outdated materials can lead to confusion and inconsistency in processes, significantly hampering compliance with ISO 9001 standards. Organizations should establish a routine review process to ensure that all documents reflect current practices and regulatory requirements, as this enhances clarity and reduces errors in operation.
Another significant challenge lies in inadequate user access and training regarding documentation systems. If employees struggle to locate or comprehend critical documents, adherence to ISO 9001 processes may falter. Organizations should prioritize comprehensive training programs that educate staff on how to navigate documentation systems effectively, ensuring easy access to essential policies and procedures that guide their daily tasks.
Analyzing the Impact of Supplier Management
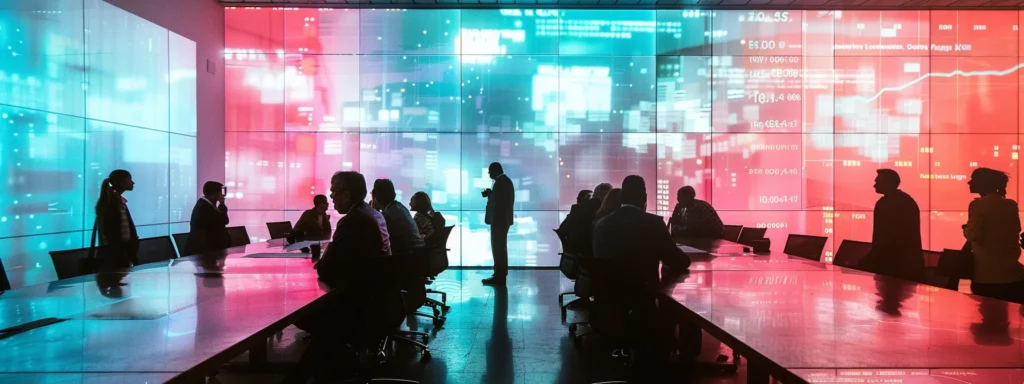
Evaluating supplier readiness for ISO compliance is critical for organizations seeking successful ISO 9001 certification. Building strong relationships with vendors not only fosters collaboration but also supports consistent quality assurance. Monitoring and measuring supplier performance helps mitigate risks associated with outsourced services. Incorporating supplier feedback into quality management enhances overall effectiveness, ensuring that organizations can seamlessly navigate their certification journey.
Evaluating Supplier Readiness for ISO Compliance
Evaluating supplier readiness for ISO compliance is essential for organizations seeking ISO 9001 certification success. Companies should perform thorough assessments to determine whether suppliers meet quality standards and can consistently deliver reliable products or services. This process often involves conducting audits and requesting documentation that demonstrates adherence to ISO guidelines, ensuring that all suppliers align with the company’s quality management objectives.
A proactive approach to supplier management includes establishing clear communication channels and fostering strong relationships with vendors. By engaging suppliers early in the certification journey, organizations can collaboratively identify areas for improvement and implement quality assurance practices that will meet ISO requirements. This partnership not only enhances supplier performance but also mitigates risks associated with noncompliance, reinforcing the company’s overall commitment to ISO 9001 standards.
Building Strong Relationships With Vendors
Building strong relationships with vendors is essential for organizations pursuing ISO 9001 certification. Companies must engage suppliers early in the process to collaboratively establish quality standards and best practices. This proactive interaction fosters trust and shared responsibility for quality, ensuring that all parties are aligned in their commitment to maintaining compliance with ISO guidelines.
Moreover, open lines of communication can facilitate swift issue resolution and feedback exchange, ultimately leading to enhanced quality assurance. Organizations that prioritize vendor relationships may see improvements in service reliability and product consistency, reducing the risks associated with non-compliance. By integrating suppliers as strategic partners, businesses can reinforce their quality management systems, significantly contributing to their ISO 9001 certification success.
Monitoring and Measuring Supplier Performance
Monitoring and measuring supplier performance is critical for organizations pursuing ISO 9001 certification, as it directly impacts the quality and reliability of products and services. Establishing clear evaluation criteria allows companies to assess whether suppliers meet the established ISO standards consistently. This ongoing assessment not only helps identify areas for improvement but also fosters open communication, ensuring that suppliers remain accountable for their contributions to the quality managementsystem.
Utilizing key performance indicators (KPIs) is an effective way for organizations to track supplier performance over time. For example, metrics such as delivery timelines, defect rates, and compliance with quality standards enable companies to gain insights into the reliability of their suppliers. By creating a systematic approach to supplier performance evaluation, organizations can mitigate risks associated with noncompliance and enhance their readiness for ISO 9001 certification.
Mitigating Risks Associated With Outsourced Services
Mitigating risks associated with outsourced services is a critical component for organizations pursuing ISO 9001 certification. Companies need to implement stringent supplier evaluation processes to ensure that vendors adhere to quality standards and regulations. By conducting regular audits and maintaining open communication, businesses can identify potential issues early on, thus safeguarding their commitment to quality management and compliance with ISO guidelines.
Another effective strategy involves developing clear contracts and performance metrics to hold suppliers accountable. This framework allows organizations to monitor supplier performance continuously and ensure that any deviations from expected quality levels are addressed promptly. By fostering strong partnerships with reliable suppliers, companies not only reduce risks but also enhance their overall quality managementsystem, ultimately supporting their journey toward ISO 9001 certification success.
Incorporating Supplier Feedback Into Quality Management
Incorporating supplier feedback into quality management is essential for organizations pursuing ISO 9001 certification. This approach enables companies to identify opportunities for enhancing processes and products by leveraging the insights of key suppliers, who often have valuable perspectives on quality improvement. For instance, by regularly engaging suppliers in performance reviews, organizations can gather critical input that informs their quality management strategies and leads to more effective compliance with ISO standards.
Furthermore, actively seeking and utilizing supplier feedback fosters a collaborative environment that strengthens relationships and promotes a shared commitment to quality. Organizations that closely monitor input from their suppliers can quickly address quality concerns and implement corrective actions, ensuring adherence to ISO 9001 requirements. This two-way communication not only streamlines the certification process but also helps organizations improve overall quality and operational efficiency, ultimately contributing to their success in achieving ISO 9001 certification.
Overcoming Financial Constraints and Budgeting Issues
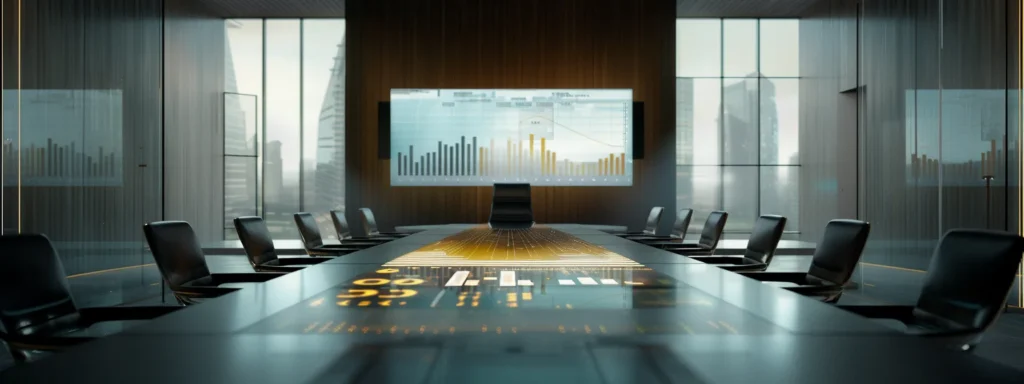
Financial constraints and budgeting issues are significant hurdles for organizations pursuing ISO 9001 certification. Estimating the costs associated with certification, prioritizing investments in quality management, and finding cost-effective training solutions are essential elements for success. Additionally, leveraging technology can help reduce certification expenses, while effective strategies for securing budget approval from management are crucial for moving forward. Each of these topics provides insights to help companies navigate their certification journey effectively.
Estimating Costs Associated With Certification
Estimating the costs associated with ISO 9001 certification can be a complex task for organizations aiming to achieve compliance while managing budgets effectively. Companies must take into account various expenses, including training for employees, the development of documentation, and the potential need for external consulting services. Accurately forecasting these costs is essential for ensuring financial preparedness and securing the necessary resources for a successful certification journey.
A practical approach to estimating certification costs involves conducting a thorough assessment of the organization’s current quality management practices. By identifying existing gaps and areas requiring improvement, companies can create a more precise budget that reflects realistic expenses needed for training, process adjustments, and documentation updates. This proactive strategy not only aids in financial planning but also highlights the commitment to quality improvement, instilling confidence among stakeholders in the pursuit of ISO 9001 certification.
Prioritizing Investments in Quality Management
Investing in quality management is essential for organizations on the path to ISO 9001 certification, particularly when facing financial constraints. Companies must identify the most impactful areas for investment, such as staff training, system upgrades, and process refinement, as these contribute significantly to achieving compliance and enhancing overall performance. A focused investment strategy not only prepares organizations for thorough audits but also fosters a culture of continuous improvement, ultimately aligning quality practices with broader business objectives.
Additionally, prioritizing financial resources for quality management can yield long-term benefits that outweigh initial costs. For example, organizations that allocate funds to enhance documentation processes and training programs often notice decreased operational errors and increased employee engagement. This proactive approach ensures that quality management becomes integrated into everyday operations, allowing companies to sustain their ISO 9001 certification and realize improved customer satisfaction over time.
Finding Cost-Effective Solutions for Training
Finding cost-effective solutions for training is essential for organizations pursuing ISO 9001 certification, especially when facing financial constraints. One practical approach involves utilizing online training platforms that offer flexible and affordable courses tailored to specific ISO standards and quality management principles. These platforms can provide employees with essential knowledge without the higher costs typically associated with in-person training sessions, making learning accessible while managing expenses effectively.
Organizations can also consider leveraging internal expertise by fostering a mentoring system where experienced employees share their knowledge about ISO 9001 standards with colleagues. This not only minimizes external training costs but also enhances team cohesion and builds a knowledgeable workforce committed to quality management. By creatively addressing training challenges, companies can ensure their teams are well-equipped to navigate the complexities of achieving ISO 9001 certification successfully.
Leveraging Technology to Reduce Certification Expenses
Leveraging technology plays a significant role in reducing expenses associated with ISO 9001 certification. Organizations can utilize quality management software that streamlines documentation processes, simplifies training, and automates compliance tracking. For instance, companies that implement an integrated system may find that it increases efficiency while decreasing manual errors, which ultimately lowers costs related to audits and ongoing compliance.
Moreover, adopting cloud-based solutions allows businesses to save on infrastructure costs while improving access to essential documents for all employees. Digital platforms facilitate real-time updates and collaborative work environments, ensuring that teams stay informed and aligned without incurring high training or operational expenses. By maximizing the use of technology, organizations can pursue ISO 9001 certification more economically, focusing resources on areas that truly impact quality and compliance.
Strategies for Securing Budget Approval From Management
Securing budget approval for ISO 9001 certification involves making a compelling business case that highlights the long-term benefits of quality management. Organizations should prepare a detailed proposal that outlines the expected return on investment, including enhanced operational efficiency, reduced operational errors, and improved customer satisfaction. By presenting data-driven insights and case studies demonstrating how successful certification has positively impacted similar companies, management can better understand the critical role quality management plays in achieving strategic goals.
Effective communication with management is essential in this process. Engaging decision-makers in discussions about the challenges faced in achieving and maintaining ISO 9001 compliance allows for addressing concerns and fostering a sense of shared responsibility. By articulating how these investments can enhance the organization’s reputation and market competitiveness, companies are more likely to secure the necessary funding and resources to initiate their certification journey and improve their overall operational standards.
Key Takeaways for Overcoming ISO 9001 Certification Challenges
Navigating the journey to ISO 9001 certification presents significant challenges for organizations, including understanding complex standards, overcoming employee resistance, and ensuring proper documentation. Proactive leadership engagement and effective training are essential for fostering a quality-driven culture that aligns with certification goals. Companies must also carefully manage supplier relationships and financial constraints to reinforce their commitment to quality management. Addressing these challenges not only enhances compliance but also drives long-term operational efficiency and customer satisfaction, making ISO 9001 certification a crucial investment for successful businesses.