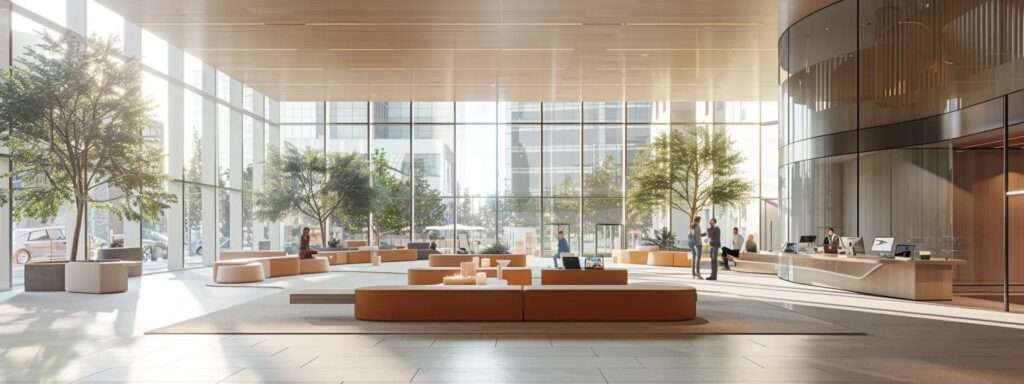
What Makes ISO 9001 Implementation Effective?
Effective ISO 9001 implementation is not just a checkbox exercise; it’s a strategic necessity for organizations looking to enhance quality and customer satisfaction. This blog post will explore the critical factors that contribute to successful implementation, including the role of leadership, the impact of organizational culture, and the importance of training and development. By addressing common challenges, such as conducting effective internal audits and achieving proper accreditation, readers will gain valuable insights to streamline their ISO processes. Engaging with this content will empower organizations to implement ISO standards more effectively, ultimately improving operational performance.
The Role of Leadership in ISO 9001 Implementation Effectiveness
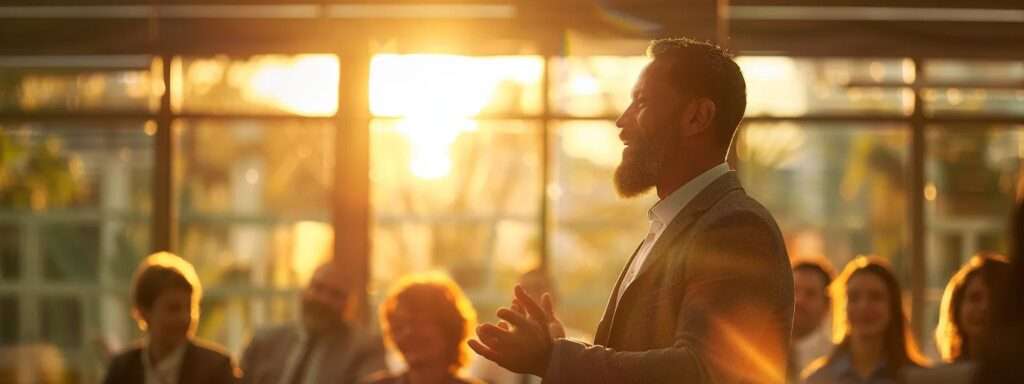
The commitment of top management significantly influences the effectiveness of ISO 9001 implementation in establishing a robust quality management system. By employing strategies for leadership engagement and actively communicating quality objectives across the organization, leaders can enhance quality assurance efforts, boost customer satisfaction, and strengthen the supply chain. This engagement lays the groundwork for successful certification and promotes a culture of continuous improvement.
The Impact of Commitment From Top Management
The dedication of top management is a fundamental element in the success of ISO 9001 implementation. Research shows that when leaders actively endorse quality management initiatives, it not only enhances adherence to regulations and standardization but also fosters a climate where employees feel valued and engaged. For example, a company that prioritizes quality by integrating it into its project management processes often sees improved operational efficiencies and customer satisfaction.
Moreover, effective leadership commitment directly influences the alignment of the organization’s goals with ISO standards. When management demonstrates a clear focus on quality objectives, it streamlines communication across all departments, ensuring everyone understands their role in achieving compliance. This unified approach reduces resistance to change and builds a shared responsibility towards maintaining high standards, ultimately leading to a culture of continuous improvement within the organization.
Strategies for Leadership Engagement
Leaders should implement clear communication channels to strengthen engagement in ISO 9001 initiatives. By routinely discussing quality management objectives during team meetings and one-on-one sessions, they reinforce the importance of meeting customer expectations. This approach ensures that everyone understands their role in compliance and prepares the team for successful audits, ultimately enhancing the organization‘s reputation for quality.
Another effective strategy involves providing leadership training focused on ISO standards and quality improvement practices. By equipping leaders with the necessary skills and knowledge, organizations can create a culture that values quality. With a strong commitment to quality management, leaders can foster an environment where employees feel empowered to contribute to continuous improvement, thus aligning practices with established creative commons license guidelines and enhancing overall operational success.
Communicating Quality Objectives Across the Organization
Effective communication of quality objectives is essential for successful ISO 9001 implementation, especially within organizations in Latin America. Leaders must ensure that these objectives align with the requirements set by the International Organization for Standardization and the ISO 9000 family standards. By clearly articulating goals related to quality and risk management, organizations foster a shared understanding among all employees, which is crucial for enhancing compliance and operational excellence.
Furthermore, engaging employees in discussions about quality objectives helps them recognize their roles in the process. This approach not only enhances accountability but also encourages employees to prioritize patient outcomes, ultimately leading to improved services and customer satisfaction. Communication must be an ongoing effort, with leaders providing feedback and addressing concerns, thereby reinforcing a culture of quality and continuous improvement throughout the organization.
Understanding Organizational Culture and Its Influence
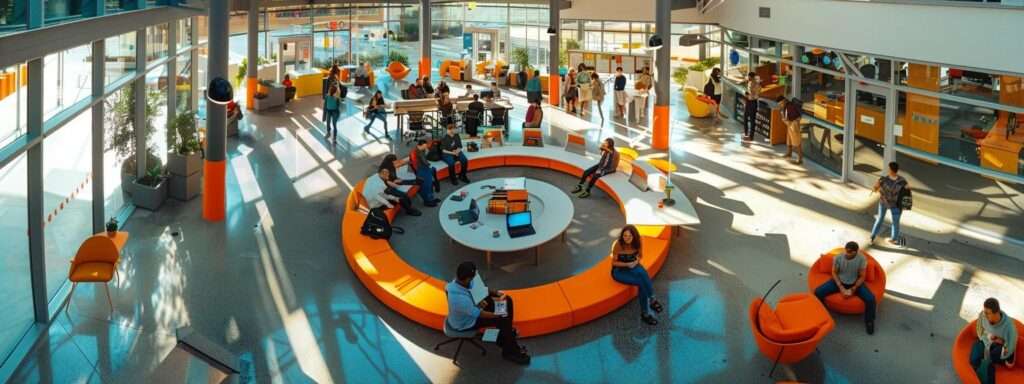
Culture significantly impacts the adoption of ISO 9001 within an organization. Aligning company values with quality management standards not only reinforces the certification process but also transforms culture into a valuable asset. Fostering a quality-conscious environment encourages employees to engage actively in the management system, which is essential for achieving lasting operational excellence.
How Culture Affects ISO 9001 Adoption
Organizational culture plays a critical role in the successful adoption of ISO 9001. A culture that emphasizes quality, continuous improvement, and employee engagement encourages staff to actively participate in quality management initiatives. Companies that integrate methodologies like Six Sigma into their operational framework often see enhanced commitment to quality processes, driving higher compliance with ISO standards and fostering a shared responsibility among employees.
Moreover, the alignment between organizational values and ISO 9001 requirements enhances the overall effectiveness of implementation. When leaders promote a culture that prioritizes quality as a core value, it leads to greater acceptance of ISO standards among the workforce. This alignment not only simplifies compliance efforts but also cultivates an environment where employees feel empowered to pursue operational excellence, ultimately contributing to improved outcomes and customer satisfaction.
Aligning Company Values With Quality Management Standards
Aligning company values with quality management standards is essential for the effective implementation of ISO 9001. When an organization integrates its core values with the principles of quality management, it creates a unified approach that fosters commitment at all levels. For instance, a firm that emphasizes customer satisfaction as a core value will likely see an enthusiastic response from employees towards quality initiatives, promoting a culture where quality becomes a shared responsibility.
This alignment not only enhances compliance with ISO standards but also drives continuous improvement throughout the organization. When leaders model behaviors that reflect these values and actively engage teams in quality-related discussions, it empowers employees to contribute more effectively. As a result, the organization can achieve its quality objectives while building a stronger reputation in the market, ultimately leading to improved customer loyalty and operational success.
Fostering a Quality-Conscious Environment
Fostering a quality-conscious environment is vital for successful ISO 9001 implementation, as it encourages employees to actively engage with quality management systems. Organizations that prioritize transparent communication about quality expectations create a culture where staff feel empowered to contribute to continuous improvement. For instance, regular training sessions focused on quality standards can increase awareness and accountability among team members, aligning their efforts with the overarching quality objectives.
Moreover, recognizing and celebrating quality achievements within the organization strengthens the commitment to maintaining high standards. When leaders publicly acknowledge efforts to meet ISO 9001 requirements, it reinforces the importance of quality across all levels and motivates employees to perform at their best. This practice not only upholds compliance but also fosters a positive environment where all employees understand their impact on operational success and customer satisfaction.
Training and Development for Successful Implementation
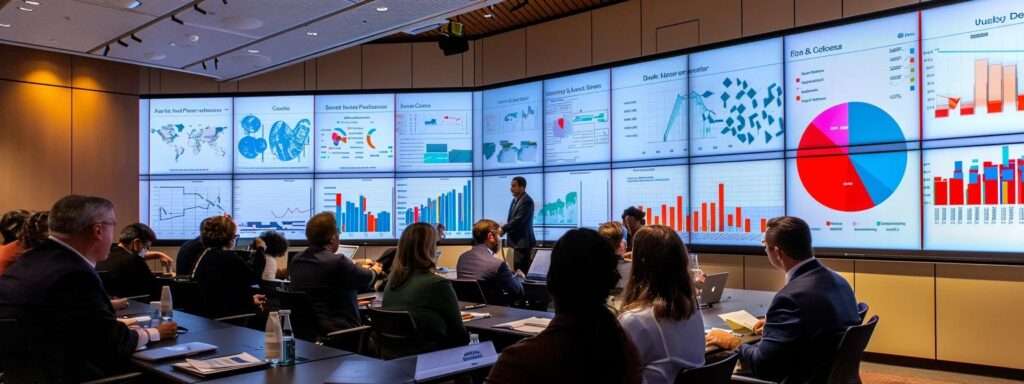
Identifying training needs is crucial for staff to ensure effective ISO 9001 implementation. Developing a targeted training program enables employees to understand quality management principles and their roles. Additionally, measuring the impact of training on quality outcomes confirms its effectiveness and supports continuous improvement initiatives. Each aspect contributes to enhanced compliance and operational success.
Identifying Training Needs for Staff
Identifying training needs for staff is a fundamental step in ensuring effective ISO 9001 implementation. Organizations should assess current skill levels and knowledge gaps related to quality management principles to tailor their training programs effectively. For example, conducting a skill assessment survey can provide insights into which areas of ISO standards require additional focus, enabling the development of targeted training sessions that enhance employees’ understanding and compliance capabilities.
Involving team members in the evaluation process also fosters a sense of ownership and accountability towards the quality management system. By gathering input from staff about their training needs, organizations can create programs that are not only relevant but also engaging. This collaborative approach not only improves training outcomes but also contributes to higher morale, ensuring that the workforce is well-equipped to support ISO 9001 initiatives and drive operational excellence.
Creating an Effective Training Program
Creating an effective training program for ISO 9001 implementation involves clearly defining the objectives and outcomes aligned with the quality management system‘s requirements. Organizations should assess the specific knowledge gaps among employees and tailor the program to address these areas. For instance, incorporating case studies related to ISO 9001 can help participants understand practical applications of the standards and their impact on achieving organizational goals.
Moreover, continuous feedback during the training process enhances the program’s effectiveness and allows adjustments as needed. Engaging employees through interactive sessions, workshops, or simulations fosters a deeper understanding of ISO principles and encourages their active participation. This approach not only reinforces the importance of quality management but also builds a strong foundation for achieving compliance and operational excellence.
Measuring Training Impact on Quality Management
Measuring the effectiveness of training programs related to ISO 9001 implementation serves as a crucial step in optimizing quality management practices. Organizations should use specific metrics, such as changes in compliance rates, customer feedback, and internal audit results, to assess how training influences operational performance. For example, if a company sees a reduction in non-conformities after a training session, it indicates that employees are better equipped to meet ISO standards.
Furthermore, regular employee evaluations and feedback sessions can provide insights into how well staff understand quality management principles post-training. By gathering data on employee performance and engagement, leadership can make informed decisions about refining training programs. These adjustments not only enhance knowledge but also strengthen the alignment of team efforts with ISO requirements, fostering a culture that values continuous improvement and operational excellence.
Process Approach and Customer Focus in ISO 9001
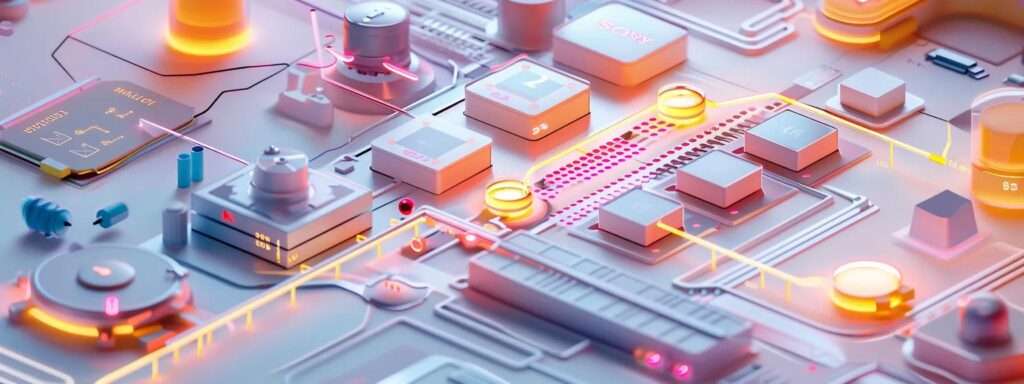
The process approach and customer focus are critical components of ISO 9001 implementation. Defining process mapping for quality management establishes a structured framework for organizational operations. Incorporating customer feedback into these processes ensures that services and products meet client expectations. Finally, continual improvement through customer satisfaction reinforces a commitment to quality that drives success, making these elements essential for effective ISO 9001 practices.
Defining Process Mapping for Quality Management
Process mapping serves as a vital tool in quality management by visually documenting workflows and highlighting interdependencies among various activities. By defining each step involved in organizational processes, businesses can identify inefficiencies and areas for improvement that impact compliance with ISO 9001 standards. For instance, a manufacturer might use process mapping to analyze the production cycle, ensuring that each stage aligns with quality objectives and stakeholder expectations, ultimately leading to enhanced operational effectiveness.
Effective process mapping not only clarifies responsibilities but also reinforces a strong customer focus within the quality management framework. When organizations map out processes with the end-user in mind, they can better anticipate customer needs and adapt procedures accordingly. By routinely integrating customer feedback into these mapped processes, companies can drive continuous improvement and maintain high standards of quality, essential for achieving ISO 9001 certification and customer satisfaction.
Incorporating Customer Feedback Into Processes
Incorporating customer feedback into processes is essential for achieving effective ISO 9001 implementation. Organizations can create channels for clients to share their insights, which allows them to understand service gaps or quality issues from the user’s perspective. For instance, a company might send out post-purchase surveys to gather direct feedback, using the collected data to refine processes, ultimately enhancing customer satisfaction and loyalty.
Moreover, aligning internal processes with customer expectations fosters a responsive organizational culture. By regularly reviewing customer feedback, organizations can adjust their operations to better meet market demands while ensuring compliance with ISO 9001 standards. This continuous improvement cycle not only strengthens quality management systems but also positions the organization to consistently exceed client expectations, a vital factor in driving long-term success.
Continual Improvement Through Customer Satisfaction
Continual improvement through customer satisfaction lies at the heart of ISO 9001 implementation. Organizations that actively solicit and analyze customer feedback can identify areas for enhancement that align with their quality objectives. For example, a company that routinely assesses survey data from clients may uncover specific needs, enabling them to refine their products and services. This proactive approach not only leads to higher quality outcomes but also fosters stronger customer loyalty.
By integrating customer insights into their operational strategies, organizations can create a culture of responsiveness and adaptability. Engaging with clients through feedback mechanisms—such as interviews or focus groups—allows businesses to maintain alignment with market demands and expectations. As a result, continual improvement becomes an ongoing practice that strengthens quality management initiatives and supports successful ISO 9001 certification.
Analyzing Case Studies of ISO 9001 Implementation
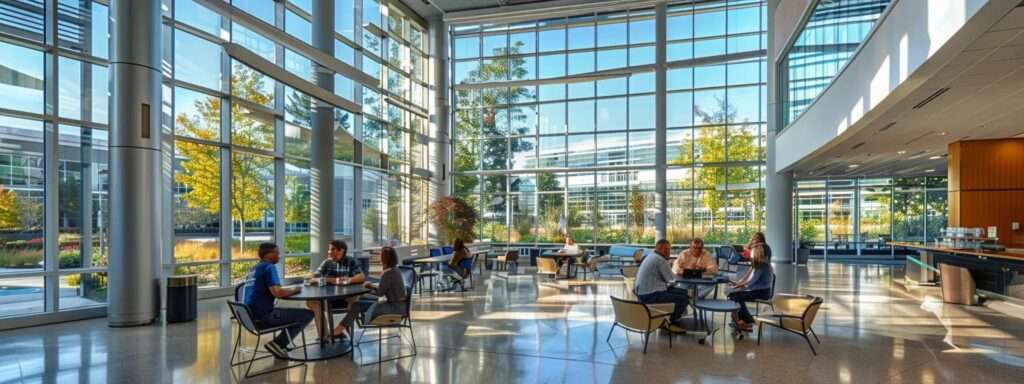
Examining case studies of ISO 9001 implementation reveals critical insights into what drives success across various sectors. This section explores success factors in real-world applications, the lessons learned from failed implementations, and comparisons of ISO 9001 outcomes across different industries. Each topic provides practical guidance that enhances understanding of effective ISO 9001 practices.
Success Factors in Real-World Applications
Successful ISO 9001 implementation often hinges on clear leadership commitment and employee engagement. In a case study of a manufacturing company, management actively promoted quality objectives through regular meetings, which resulted in a significant increase in staff involvement in quality initiatives. This leadership support not only fostered an organizational culture of quality but also enhanced compliance with ISO standards, ultimately driving improvements in customer satisfaction and operational efficiency.
Another critical factor is the integration of customer feedback into quality management processes. For instance, a service-oriented organization that utilized customer surveys to gather insights was able to identify specific areas for enhancement. By responding to client needs, the company improved service delivery, leading to higher ratings in customer satisfaction and reinforcing its commitment to continual improvement, a core principle of ISO 9001.
Lessons Learned From Failed Implementations
Analyzing failed ISO 9001 implementations reveals common pitfalls that organizations should avoid to enhance their chances of success. For instance, a lack of leadership commitment often leads to inadequate resource allocation and employee disengagement, resulting in poor adherence to quality standards. One notable case involved a manufacturing firm that attempted to implement ISO 9001 without proper training for its staff, ultimately leading to confusion about processes and failure to meet certification requirements.
Another lesson from unsuccessful implementations is the importance of involving all employees in the quality management journey. A service organization that overlooked employee insights during the ISO 9001 process faced resistance and low morale, which hindered overall program effectiveness. By fostering a culture of open communication and including employee feedback, organizations can better navigate challenges and create a more robust foundation for sustained quality improvement.
Comparing ISO 9001 Results Across Different Industries
Comparing ISO 9001 results across different industries highlights the varying impacts of certification on organizational performance. For instance, in the manufacturing sector, companies often notice significant improvements in process efficiency and waste reduction after implementing ISO 9001 standards. In contrast, service-oriented industries may experience enhanced customer satisfaction and loyalty, demonstrating how specific benefits of ISO 9001 can differ based on the nature of the business.
The differences in results also stem from how each industry prioritizes quality management. In healthcare, for instance, adopting ISO 9001 can lead to better patient outcomes through improved service delivery and compliance with safety standards. Conversely, the technology sector might focus more on innovation and risk management, finding that ISO 9001 provides a framework for maintaining quality while driving product development. This variance underscores the need for organizations to adapt ISO 9001 implementation to their unique demands and goals to maximize its effectiveness.
Tools and Techniques Supporting ISO 9001 Effectiveness
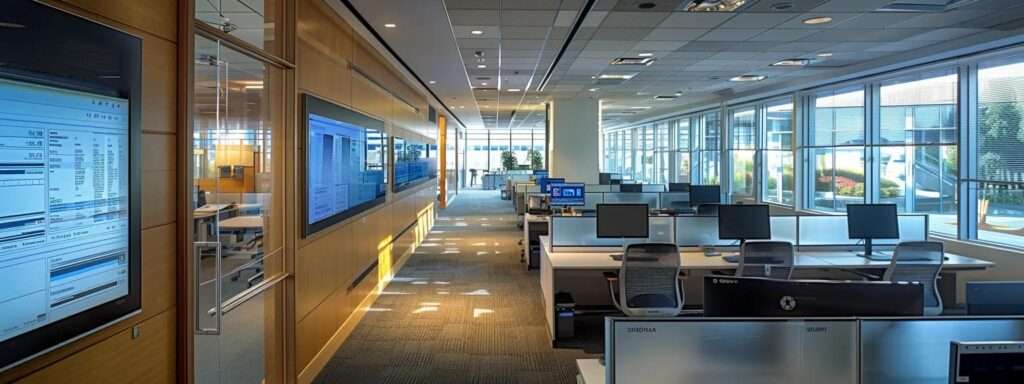
Utilizing quality management software streamlines ISO 9001 processes, enhancing efficiency and data accuracy. Implementing data analysis techniques empowers organizations to make informed decisions, improving overall quality performance. Additionally, regular auditing serves as a vital tool for continuous improvement, identifying areas for advancement and ensuring compliance. Each of these elements plays a crucial role in achieving effective ISO 9001 implementation.
Utilizing Quality Management Software
Utilizing quality management software is essential for organizations aiming to achieve effective ISO 9001 implementation. This type of software often includes tools for document control, audit management, and corrective action tracking, all of which streamline processes and ensure compliance with ISO standards. For instance, a company using such software can easily manage updates to its quality documentation and maintain an accurate record of employee training, reducing the risk of errors that could lead to compliance issues.
Furthermore, relying on quality management software enhances data-driven decision-making by providing real-time insights into quality performance metrics. This capability allows organizations to identify trends and areas needing improvement promptly. For example, if an organization detects an increase in customer complaints through software analytics, it can take immediate corrective action to address the underlying issues, ultimately leading to higher customer satisfaction and better alignment with ISO 9001 requirements.
Implementing Data Analysis Techniques
Implementing data analysis techniques is a critical aspect of effective ISO 9001 execution, as it allows organizations to evaluate performance metrics and identify trends that impact quality management. By leveraging data analytics, businesses can pinpoint inefficiencies in their processes, enabling them to take informed actions to enhance compliance and customer satisfaction. For instance, analyzing defect rates over time can reveal patterns, allowing teams to address root causes and refine their quality assurance measures.
Furthermore, organizations can benefit from utilizing software tools that facilitate data collection and analysis, streamlining efforts to meet ISO 9001 standards. These tools offer real-time insights into quality-related performance, helping leaders make proactive decisions based on reliable information. For example, a company that tracks customer feedback through data analysis can swiftly identify areas needing improvement, fostering a culture of continuous enhancement and aligning its operations with the requirements of ISO 9001.
Auditing as a Tool for Continuous Improvement
Auditing serves as a vital component in the continuous improvement of ISO 9001 implementation, providing organizations with the opportunity to assess compliance and identify areas for enhancement. Through regular internal and external audits, companies can evaluate their quality management systems, ensuring they align with ISO standards. For instance, a manufacturing firm that conducts thorough audits may uncover inefficiencies in their production processes, prompting immediate corrective measures that enhance overall operational performance.
Moreover, the insights gained from audits can drive informed decision-making and foster a culture of accountability. By analyzing audit findings, organizations can set specific goals for improvement and track progress over time. This proactive approach not only strengthens compliance with ISO 9001 requirements but also demonstrates a commitment to quality that resonates with customers and stakeholders, ultimately contributing to increased satisfaction and loyalty.
Key Takeaways for Successful ISO 9001 Implementation
Effective ISO 9001 implementation hinges on strong leadership commitment, employee engagement, and a culture that prioritizes quality. Organizations that align their values with quality management standards create an environment conducive to continuous improvement and operational excellence. By regularly incorporating customer feedback and utilizing data-driven decision-making, businesses can enhance compliance and overall performance. Emphasizing these elements not only solidifies adherence to ISO standards but also fosters lasting customer satisfaction and loyalty.